GranuLac: The perfect product for your granulation process!
MEGGLE has it.
The right lactose product for wet and dry granulation
In many industries particle size enlargement is the most important process by far, because “usability of product” can be improved significantly.
In such a particle design process primary, smaller particles are brought together forming larger, multivariate entities of desired properties, agglomerates or granules. The fundamental advantage of such an agglomeration step is – besides a meaningful increase in density – an improved flowability. Most important for inhomogeneous blends is a stoichiometric ratio of the involved components insuring content and weight uniformity.
Processes: Wet and dry granulation
Basically, granulation can be handled in a wet or dry manner: Particles may be either “glued” together using sticky or solving liquids like fluid binders or aqueous/organic solvents (wet granulation). Alternatively, pressure may be applied to increase particle size (dry granulation). Platforms for wet granulation procedures are classical wet granulation processes, consisting of e.g. a high shear granulator (HSWG) or a fluid bed (FBWG), drying equipment, and/or sieves. In dry granulation a roller compactor, or sporadically a heavy duty tablet press (slugging) are consulted. Roller compaction has become the preferred technology for it is a semi-continuous process, amenable to process analytical tools, with greater throughput and yields, and with lower absolute running areas needed.
Suitable for continuous manufacturing
A special version is moisture activated dry granulation (MADG), where only a minimum of liquid binder is used, avoiding interaction with formulation components susceptible to water/solvent. In classical direct compression (DC) pre-treated excipients insure sufficient powder flow, formation of compacts, and content uniformity of a blend a priori, so that ideally only one blending step is needed before compaction. Practically, this procedure is of great economical interest for the overall number of working steps is strongly reduced. As a consequence there is less investment in GMP space, labor, maintenance, or validation work needed. As DC is a dry operation, stability of formulation components is less challenging, and there is less energy consumption, for drying is omitted. Particles mainly stick together by weak van der Waals forces resulting in a rapid disintegration after administration. All granulation platforms are suitable for continuous manufacturing.
MEGGLE’s lactose grades suitable for granulation are available under the trade names GranuLac® 70, GranuLac® 80 GranuLac® 140, GranuLac® 200, GranuLac® 230, SorboLac® 400,
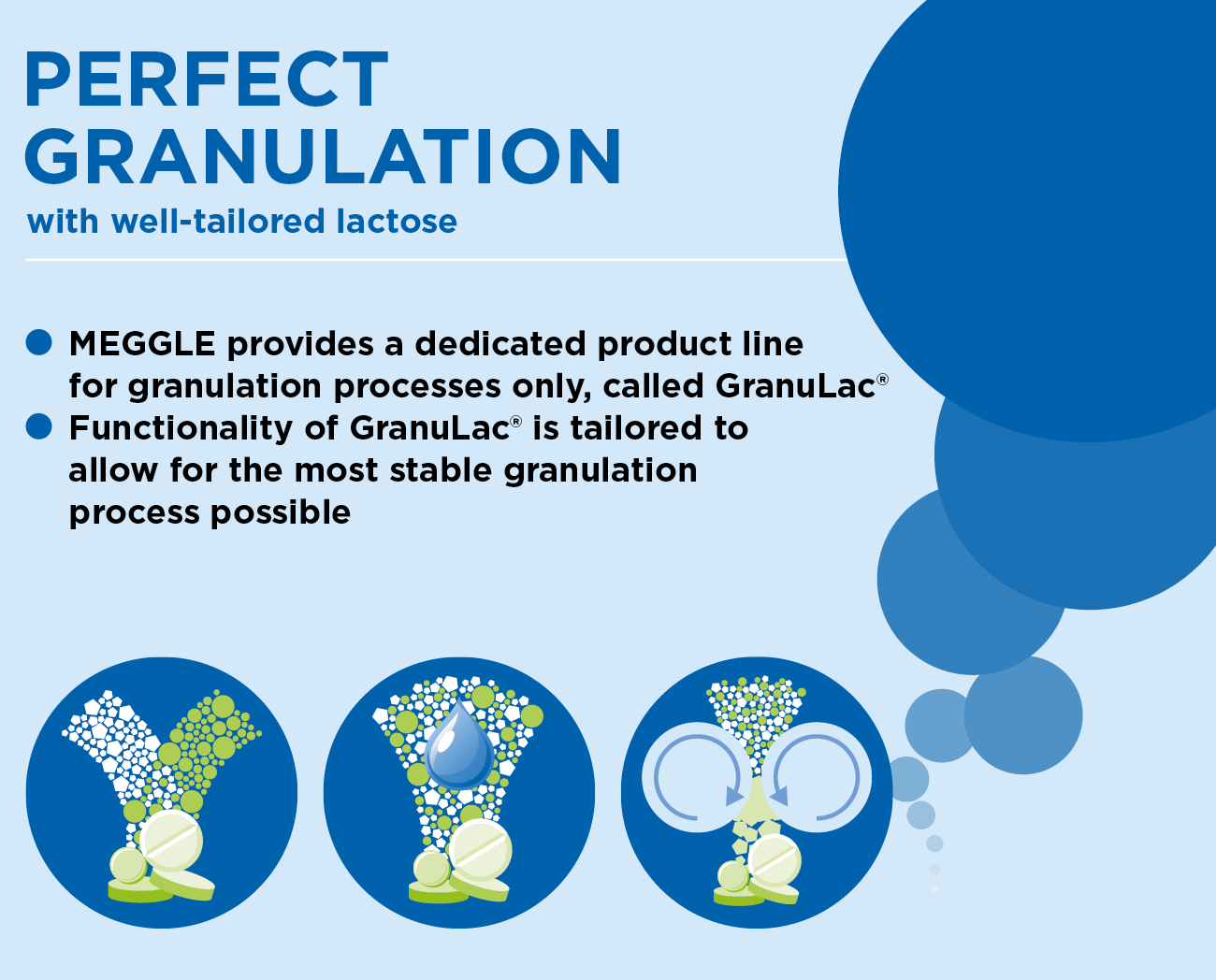
Information / Sample request:
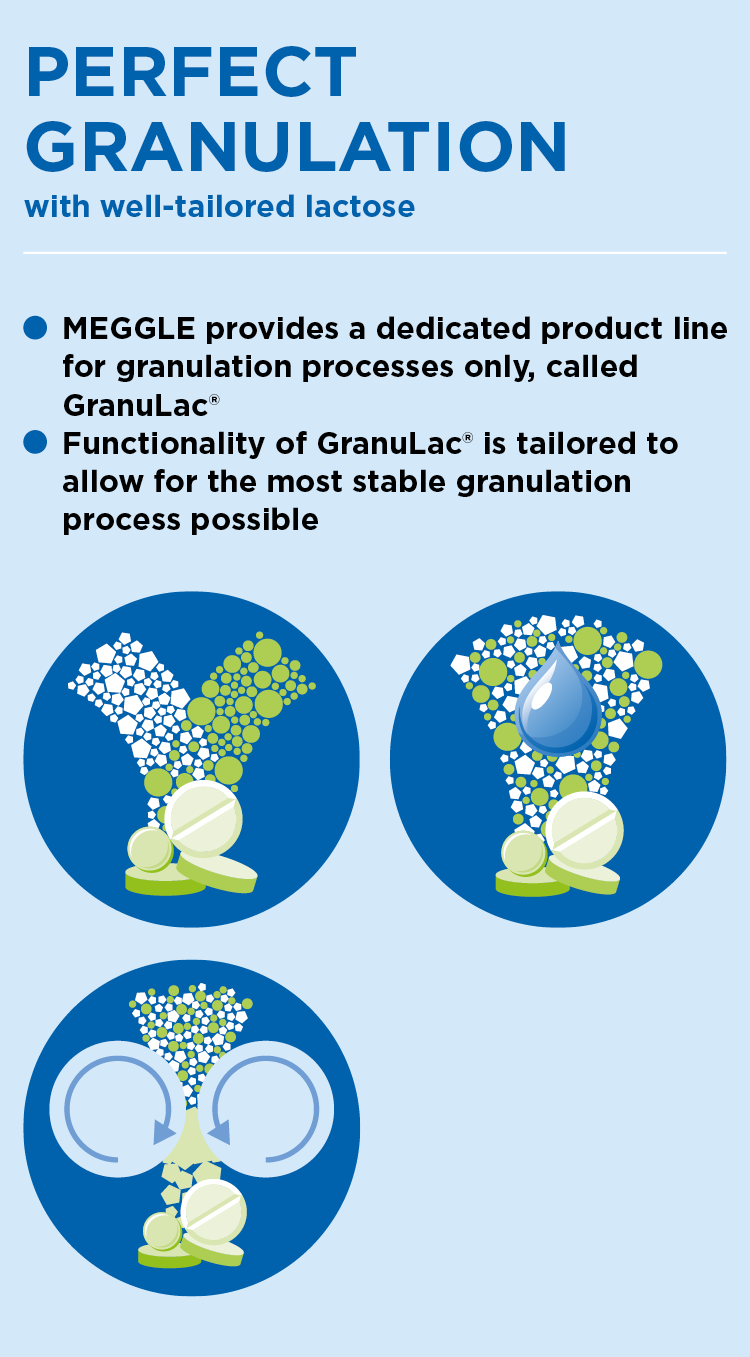
MEGGLE has it.
The right lactose product for wet and dry granulation
In many industries particle size enlargement is the most important process by far, because “usability of product” can be improved significantly.
In such a particle design process primary, smaller particles are brought together forming larger, multivariate entities of desired properties, agglomerates or granules. The fundamental advantage of such an agglomeration step is – besides a meaningful increase in density – an improved flowability. Most important for inhomogeneous blends is a stoichiometric ratio of the involved components insuring content and weight uniformity.
Processes: Wet and dry granulation
Basically, granulation can be handled in a wet or dry manner: Particles may be either “glued” together using sticky or solving liquids like fluid binders or aqueous/organic solvents (wet granulation). Alternatively, pressure may be applied to increase particle size (dry granulation). Platforms for wet granulation procedures are classical wet granulation processes, consisting of e.g. a high shear granulator (HSWG) or a fluid bed (FBWG), drying equipment, and/or sieves. In dry granulation a roller compactor, or sporadically a heavy duty tablet press (slugging) are consulted. Roller compaction has become the preferred technology for it is a semi-continuous process, amenable to process analytical tools, with greater throughput and yields, and with lower absolute running areas needed.
Suitable for continuous manufacturing
A special version is moisture activated dry granulation (MADG), where only a minimum of liquid binder is used, avoiding interaction with formulation components susceptible to water/solvent. In classical direct compression (DC) pre-treated excipients insure sufficient powder flow, formation of compacts, and content uniformity of a blend a priori, so that ideally only one blending step is needed before compaction. Practically, this procedure is of great economical interest for the overall number of working steps is strongly reduced. As a consequence there is less investment in GMP space, labor, maintenance, or validation work needed. As DC is a dry operation, stability of formulation components is less challenging, and there is less energy consumption, for drying is omitted. Particles mainly stick together by weak van der Waals forces resulting in a rapid disintegration after administration. All granulation platforms are suitable for continuous manufacturing.
MEGGLE’s lactose grades suitable for granulation are available under the trade names GranuLac® 70, GranuLac® 80 GranuLac® 140, GranuLac® 200, GranuLac® 230, SorboLac® 400,